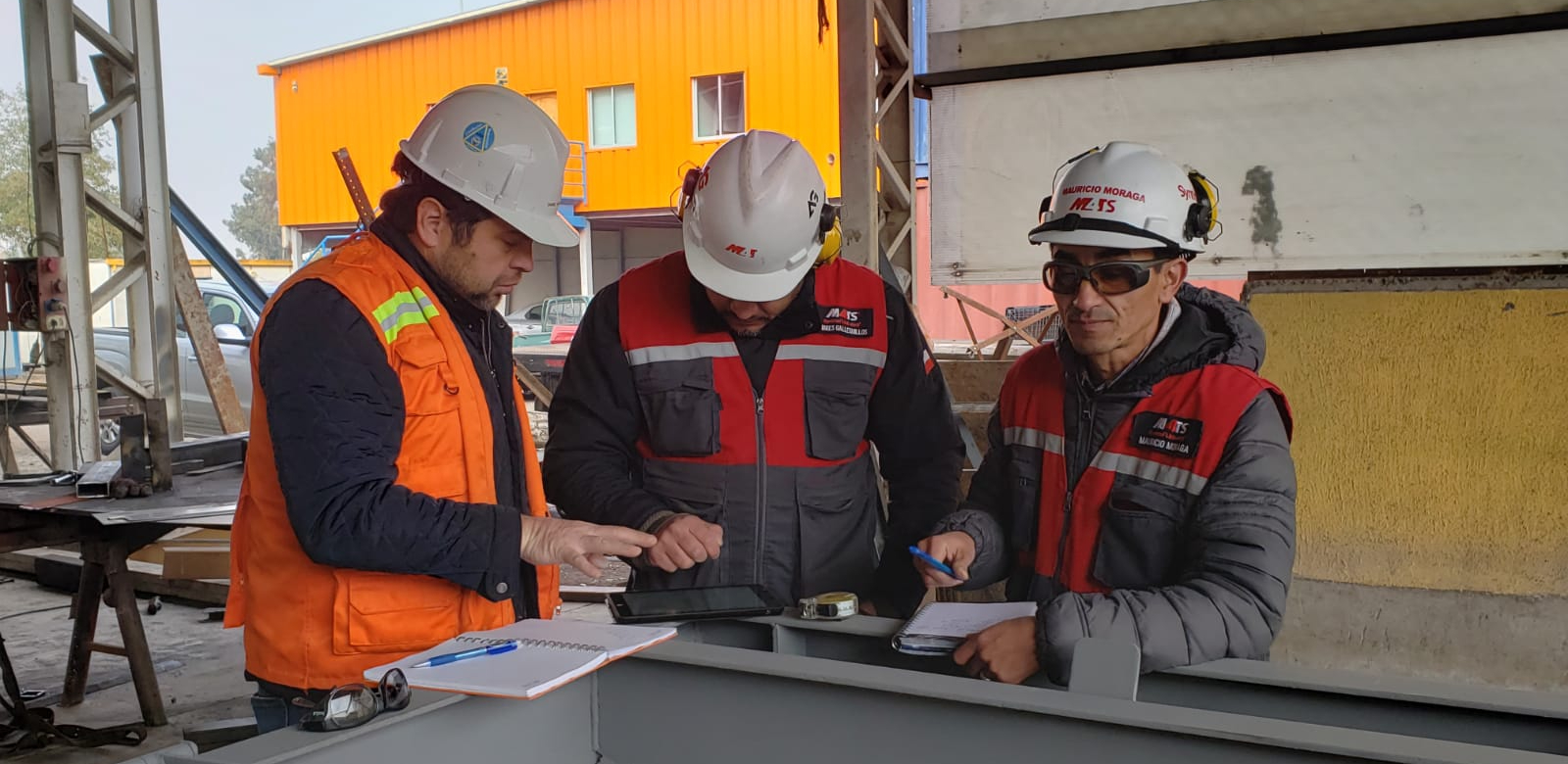
Field Services
Is your equipment producing strange noises? Have you observed changes in its regular operation? Is something not quite right? When encountering an issue, let an M4TS technician inspect and assess your equipment to guarantee accurate diagnosis and the optimal solution.
Our field service technicians and engineers are available 24/7 to address all your needs. Whether it’s installation supervision, field inspections, mechanical repairs, or process evaluation and tuning, our team will help ensure your operations run efficiently and smoothly.
.
Commissioning Assistance
M4TS will conduct a site visit before machine start-up to verify correct installation and operation of your equipment, providing a detailed report with necessary action items. This service also includes training sessions for plant employees (refer to the Training section for details).
We offer multi-visit options for customers who require on-site assistance more than once (e.g., an initial visit during installation to ensure proper machine placement, followed by another visit closer to start-up to review machine operation and conduct training with the end user).
A pre-operation inspection instills confidence that your equipment will perform as expected without causing machine or structural damage.
NOTE: M4TS does not provide machine installation services. This pre-operation inspection is conducted after machine installation.
Predictive Maintenance Assessment
M4TS will conduct a thorough inspection of your equipment prior to your next scheduled shutdown, allowing you to address any issues during that time. A predictive maintenance assessment gives you the opportunity to prepare and order parts, aiding in resource allocation and minimizing or eliminating downtime and profit loss from unforeseen problems.
This assessment includes a review of general equipment operation and performance, recommendations for significant repairs or replacements, an evaluation of the maintenance program, and a comprehensive inspection report.
NOTE: The predictive maintenance assessment necessitates an equipment shutdown for approximately one hour or more to thoroughly examine the equipment and complete the inspection.
.
Repair Supervision
M4TS will oversee the repair or replacement of components to guarantee correct installation and prevent further issues or downtime.
NOTE: This service is supervisory only. The customer must supply all manpower and equipment needed to carry out the repair.
Training
Proper machine maintenance results in reduced downtime and increased production, so it’s essential for your employees to know how to keep your equipment running smoothly and efficiently.
Our training offering includes both classroom learning and hands-on sessions with the machine. Topics covered include system components, preventive maintenance, parts replacement, and basic troubleshooting
M4TS LLC.
1925 Lovering Ave
Wilmington, DE 19806
Delaware - United States
US Phone: +19452340499
Email: [email protected]
M4TS SpA
Callao 2970 Office 704
Las Condes - Santiago
Chile
Phone: + 56 22234418
Email: [email protected]
M4TS ATLANTICA SRL
Carlos Quijano 1290 Office 101
Montevideo - Uruguay
Email: [email protected]